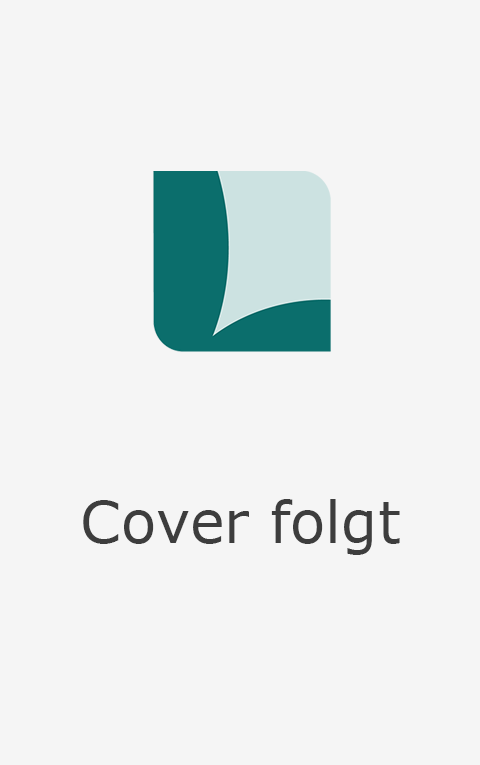
Metallurgy and Corrosion Control in Oil and Gas Production
John Wiley & Sons Inc (Verlag)
978-1-119-25205-4 (ISBN)
This book discusses upstream operations, with an emphasis on production, and pipelines, which are closely tied to upstream operations. It also examines protective coatings, alloy selection, chemical treatments, and cathodic protection—the main means of corrosion control. The strength and hardness levels of metals is also discussed, as this affects the resistance of metals to hydrogen embrittlement, a major concern for high-strength steels and some other alloys. It is intended for use by personnel with limited backgrounds in chemistry, metallurgy, and corrosion and will give them a general understanding of how and why corrosion occurs and the practical approaches to how the effects of corrosion can be mitigated.
Metallurgy and Corrosion Control in Oil and Gas Production, Second Edition updates the original chapters while including a new case studies chapter. Beginning with an introduction to oilfield metallurgy and corrosion control, the book provides in-depth coverage of the field with chapters on: chemistry of corrosion; corrosive environments; materials; forms of corrosion; corrosion control; inspection, monitoring, and testing; and oilfield equipment.
Covers all aspects of upstream oil and gas production from downhole drilling to pipelines and tanker terminal operations
Offers an introduction to corrosion for entry-level corrosion control specialists
Contains detailed photographs to illustrate descriptions in the text
Metallurgy and Corrosion Control in Oil and Gas Production, Second Edition is an excellent book for engineers and related professionals in the oil and gas production industries. It will also be an asset to the entry-level corrosion control professional who may have a theoretical background in metallurgy, chemistry, or a related field, but who needs to understand the practical limitations of large-scale industrial operations associated with oil and gas production.
Robert Heidersbach, PhD, is the President of Dr. Rust, Inc., a consulting firm that specializes in corrosion, metallurgy, and materials consulting for a variety of international clients, including oil and gas production, military hardware, construction, litigation, and failure analysis. He was previously a faculty member in ocean engineering at the University of Rhode Island, chemical engineering at Oklahoma State, and metallurgy and materials engineering at California Polytechnic State University.
Preface xiii
1 Introduction to Oilfield Metallurgy and Corrosion Control 1
Costs, 1
Safety, 2
Environmental Damage, 2
Corrosion Control, 3
References, 3
2 Chemistry of Corrosion 5
Electrochemistry of Corrosion, 5
Electrochemical Reactions, 5
Electrolyte Conductivity, 6
Faraday’s Law of Electrolysis, 6
Electrode Potentials and Current, 6
Corrosion Rate Expressions, 10
pH, 10
Passivity, 11
Potential‐pH (Pourbaix) Diagrams, 11
Summary, 12
References, 12
3 Corrosive Environments 15
External Environments, 16
Atmospheric Corrosion, 17
Water as a Corrosive Environment, 18
Soils as Corrosive Environments, 20
Corrosion Under Insulation, 21
Internal Environments, 24
Crude Oil, 24
Natural Gas, 25
Oxygen, 26
Carbon Dioxide, 26
Hydrogen Sulfide, 29
Organic Acids, 32
Scale, 33
Microbially Influenced Corrosion (MIC), 36
Mercury, 41
Hydrates, 41
Fluid Flow Effects on Corrosion, 41
Summary, 41
References, 42
4 Materials 47
Metallurgy Fundamentals, 47
Crystal Structure, 47
Material Defects, Inclusions, and Precipitates, 48
Strengthening Methods, 50
Mechanical Properties, 51
Forming Methods, 60
Castings, 60
Wrought Metal Products, 60
Welding, 61
Clad Metals, 65
Additive Manufacturing, 65
Materials Specifications, 65
API – The American Petroleum Institute, 66
AISI – The American Iron and Steel Institute, 66
ASTM International (Formerly the American Society for Testing and Materials), 66
ASME – The American Society of Mechanical Engineers, 67
SAE International (Formerly the Society of Automotive Engineers), 67
UNS – The Universal Numbering System, 67
NACE – The Corrosion Society (Formerly the National Association of Corrosion Engineers), 68
Other Organizations, 68
Use of Materials Specifications, 68
Carbon Steels, Cast Irons, and Low‐Alloy Steels, 69
Classifications of Carbon Steels, 71
Alloying Elements and Their Influence on Properties of Steel, 72
Strengthening Methods for Carbon Steels, 74
Quench and Tempered (Q&T) Steels, 75
Carbon Equivalents and Weldability, 76
Cleanliness of Steel, 76
Cast Irons, 76
Corrosion‐Resistant Alloys (CRAs), 77
Iron–Nickel Alloys, 77
Stainless Steels, 78
Nickel‐based Alloys, 83
Cobalt‐based Alloys, 84
Titanium Alloys, 84
Copper Alloys, 86
Aluminum Alloys, 89
Additional Considerations with CRAs, 91
Polymers, Elastomers, and Composites, 93
Materials Selection Guidelines, 97
References, 97
5 Forms of Corrosion 101
Introduction, 101
General Corrosion, 102
Galvanic Corrosion, 104
Galvanic Coupling of Two or More Metals, 104
Area Ratio, 105
Metallurgically Induced Galvanic Corrosion, 107
Environmentally Induced Galvanic Corrosion, 109
Polarity Reversal, 111
Conductivity of the Electrolyte, 111
Control of Galvanic Corrosion, 111
Pitting Corrosion, 112
Occluded Cell Corrosion, 113
Pitting Corrosion Geometry and Stress Concentration, 114
Pitting Initiation, 115
Pitting Resistance Equivalent Numbers (PRENs), 115
Pitting Statistics, 116
Prevention of Pitting Corrosion, 117
Crevice Corrosion, 117
Corrosion Under Pipe Supports (CUPS), 119
Pack Rust, 120
Crevice Corrosion Mechanisms, 121
Alloy Selection, 121
Filiform Corrosion, 122
Intergranular Corrosion, 123
Stainless Steels, 123
Corrosion Parallel to Forming Directions, 124
Aluminum, 124
Other Alloys, 125
Dealloying, 125
Mechanism, 125
Selective Phase Attack, 126
Susceptible Alloys, 126
Control, 126
Erosion Corrosion, 127
Mechanism, 127
Velocity Effects and ANSI/API RP14E, 128
Materials, 130
Cavitation, 130
Areas of Concern, 131
Erosion and Erosion‐corrosion Control, 133
Environmentally Assisted Cracking, 134
Stress Corrosion Cracking (SCC), 135
Hydrogen Embrittlement and H2S‐related Cracking, 139
Liquid Metal Embrittlement (LME), 143
Corrosion Fatigue, 143
Other Forms of Corrosion Important to Oilfield Operations, 145
Oxygen Attack, 145
Sweet Corrosion, 145
Sour Corrosion, 145
Mesa Corrosion, 145
Top‐of‐Line (TOL) Corrosion, 145
Channeling Corrosion, 146
Grooving Corrosion: Selective Seam Corrosion, 148
Wireline Corrosion, 148
Additional Forms of Corrosion Found in Oil and Gas Operations, 148
Additional Comments, 152
References, 153
6 Corrosion Control 159
Protective Coatings, 159
Paint Components, 159
Coating Systems, 160
Corrosion Protection by Paint Films, 160
Desirable Properties of Protective Coating Systems, 161
Developments in Coatings Technology, 162
Surface Preparation, 162
Purposes of Various Coatings, 166
Generic Binder Classifications, 167
Coatings Suitable for Various Service Environments or Applications, 169
Coatings Inspection, 169
Areas of Concern and Inspection Concentration, 174
Linings, Wraps, Greases, and Waxes, 176
Coatings Failures, 180
Metallic Coatings, 189
Useful Publications, 192
Water Treatment and Corrosion Inhibition, 192
Oil Production Techniques, 193
Water Analysis, 193
Gas Stripping and Vacuum Deaeration, 194
Corrosion Inhibitors, 194
Cathodic Protection, 199
How Cathodic Protection Works, 201
Types of Cathodic Protection, 203
Cathodic Protection Criteria, 214
Inspection and Monitoring, 216
Cathodic Protection Design, 220
Additional Topics Related to Cathodic Protection, 224
Summary of Cathodic Protection, 227
Standards for Cathodic Protection, 227
References, 228
7 Inspection, Monitoring, and Testing 233
Inspection, 235
Visual Inspection (VT), 235
Penetrant Testing (PT), 236
Magnetic Particle Inspection (MT), 237
Ultrasonic Inspection (UT), 237
Radiography (RT), 238
Eddy Current Inspection, 240
Magnetic Flux Leakage (MFL) Inspection, 241
Positive Material Identification (PMI), 242
Thermography, 242
Additional Remarks About Inspection, 243
Monitoring, 244
Monitoring Probes, 244
Electrochemical Corrosion Rate Monitoring Techniques, 250
Hydrogen Probes, 253
Sand Monitoring, 254
Fluid Analysis, 255
Naturally Occurring Radioactive Materials (NORM), 257
Additional Comments on Monitoring, 258
Testing, 258
Hydrostatic Testing, 258
Laboratory and Field Trial Testing, 260
References, 262
8 Oilfield Equipment 265
Drilling and Exploration, 265
Drill Pipe, 265
Tool Joints, 268
Blowout Preventers (BOPs), 268
Wells and Wellhead Equipment, 269
History of Production, 270
Downhole Corrosive Environments, 271
Annular Spaces, 275
Types of Wells, 275
Tubing, Casing, and Capillary Tubing, 277
Corrosion Inhibitors for Tubing and Casing in Production Wells, 280
Internally Coated Tubing for Oilfield Wells, 283
Wireline, 285
Coiled Tubing, 285
Material and Corrosion Concerns with Artificial Lift Systems, 286
Facilities and Surface Equipment, 291
Piping, 291
Storage Tanks, 293
Heat Exchangers, 297
Other Equipment, 301
Bolting, Studs, and Fasteners, 301
Problems with Bolted Connections, 306
International Bolting Standards, 307
Flares, 312
Corrosion Under Insulation, 312
Pipelines and Flowlines, 319
Pipeline Problems and Failures, 319
Forms of Corrosion Important in Pipelines and Flowlines, 321
Repairs and Derating Due to Corrosion, 323
Casings for Road and Railway Crossings, 323
Pipeline and Flowline Materials, 324
Pipeline Hydrotesting, 326
Seawater Injection Pipelines/Flowlines, 327
External Corrosion of Pipelines, 327
Internal Corrosion of Pipelines, 330
Inspection, Condition Assessment, and Testing, 332
Offshore and Marine Applications, 336
Offshore Pipelines, 336
Offshore Structures, 337
References, 342
Index
Erscheinungsdatum | 26.09.2018 |
---|---|
Reihe/Serie | Wiley Series in Corrosion |
Verlagsort | New York |
Sprache | englisch |
Maße | 216 x 274 mm |
Gewicht | 1247 g |
Themenwelt | Naturwissenschaften ► Chemie |
Technik ► Bergbau | |
Technik ► Elektrotechnik / Energietechnik | |
Technik ► Maschinenbau | |
ISBN-10 | 1-119-25205-9 / 1119252059 |
ISBN-13 | 978-1-119-25205-4 / 9781119252054 |
Zustand | Neuware |
Haben Sie eine Frage zum Produkt? |
aus dem Bereich